Use Traceability to the Advantage of Food Quality Control
Here on our blog, we never tire of talking about the importance of traceability associated with quality control, specifically quality inspections, both of products and of a company's processes.
When we talk about retailers, we often hear the same question...
What influence does a tracked product base have on quality inspection?
Before answering this question, delving deeper into the concept of "quality inspection" is relevant.
Inspecting the quality of a product is to technically evaluate it, based on pre-established parameters in specifications (in the case of fruits, vegetables and greens, we can evaluate dimension, color, percentage of mild and severe defects, percentage of rottenness, among others), a sample of the products when received, shipped or at stores, to ensure the standardization of quality.
At first, this process might seem complicated, and it might be, but this is directly connected with the level of quality that your company wishes to offer to the market.
Your business can be recognized by the market for its excellence in the quality of products and services, and create a connection with customers and consumers, or as just another company or brand with no unique features. You can fight for price or for value, you decide.
The point is that the market no longer has room for companies and brands that don’t reinvent themselves. Therefore, it’s up to you alone to decide which path to follow.
Technology as an ally
In this sense, after many conversations with our customers, we developed the CLICQ solution for Inspection and Quality Control checklists, which automates the collection of quality inspection data, and can be linked to the traceability code, which allows the identification of the source of the product being inspected.
Remembering that quality inspection can take place during the reception, storage, or shipping by the distributor, at the distribution center, or even at the stores.
In other post, "How to make money with Quality Control", we talked about the relationship between an excellent level of control points and costs, i.e. controlling a lot can generate high costs, however, controlling nothing or very little generates uncertainty and imprecision in the analysis. See the chart below:
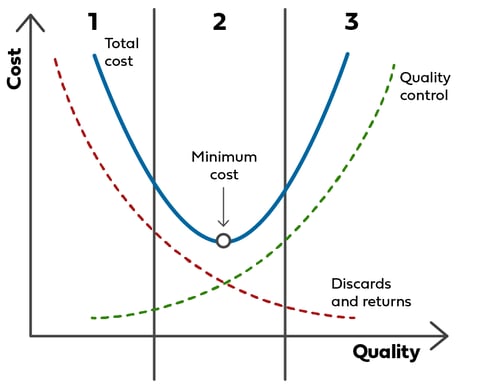
Finding the balance within this process lies in defining the control points according to your company's capacity to execute, it is possible to improve the data collection process and expand the coverage of inspections with the use of traceability, without necessarily increasing the number of inspectors or infrastructure, and without increasing operational costs.
How it works
Suppliers that have the Tracker System, developed by PariPassu, must send their products identified by the label with the tracking code, which provides a set of information, such as source, product, total weight, total number of boxes, and other information that serves as input for the CLICQ application, to check the initial analysis parameters automatically, according to the needs of each company.
Reading this information at the very beginning of the inspection eliminates the need to identify who the supplier is, what the product is, the quantity analyzed, and what the evaluation limits are - all this information is automatically loaded into CLICQ - optimizing the team's time, allowing the number of inspections to be increased, which will guarantee the quality standard of the products.
Result
On average, for every percentage point increase in coverage in the tracked volume, the number of quality inspections increases between 1.2 and 1.7 percentage points. This rate varies according to the complexity of the parameters established for quality inspections.
With more inspections, which identify not only the direct supplier, but also the source of the product, it’s possible to outline a development and management plan for suppliers, focusing on the receipt of products that are more suitable to the expected standard and, consequently, the reduction of stock-out at the point of sale.
+Content
We have listed additional content that you will enjoy:
- 5 most widely used types of Quality Management indicators